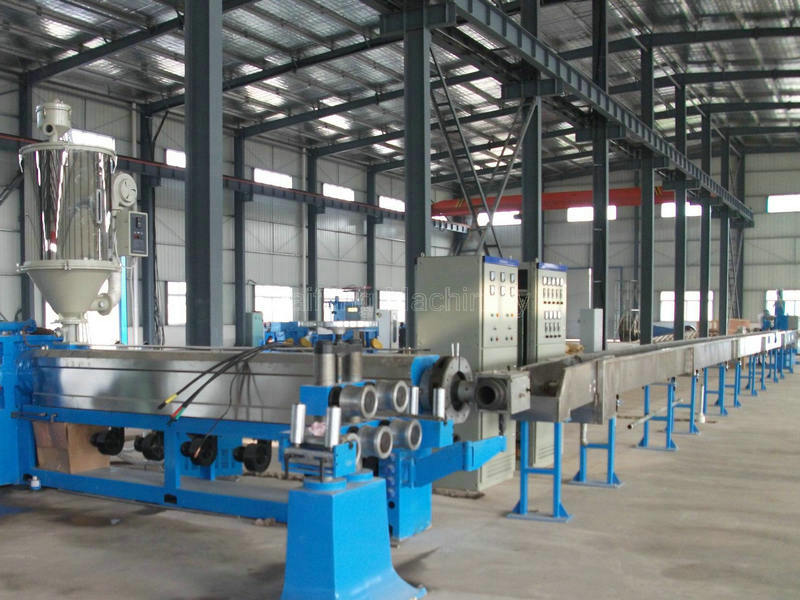
在當今工業制造領域,聚碳酸酯(PC)由于其優越的透明性、抗沖擊性和加工性能,廣泛應用于汽車制造、建筑材料、電子產品等多個領域。而PC擠出機作為生產過程中不可或缺的設備,通過精確控制溫度和壓力,將PC顆粒加工成各種規格的型材產品。了解PC擠出機的生產工藝流程圖,對于提高產品質量、優化生產效率具有重要意義。
PC擠出機的生產工藝流程可以分為以下幾個階段:
- 原料準備:選擇合適規格的PC顆粒作為原材料。這些顆粒通常需要經過干燥處理以除去水分,防止在擠出過程中發生降解或產生氣泡。
- 加料:將干燥后的PC顆粒通過加料口送入擠出機的料斗中。現代擠出機通常配備自動上料系統,以確保連續穩定的供料。
- 擠壓成型:PC顆粒在擠出機內被加熱至熔點以上的溫度,并在螺桿的旋轉推動下向前移動,逐漸塑化形成均勻的熔融狀態。這一過程對溫度和速度的控制至關重要,直接影響到最終產品的質量和性能。
- 模具成型:熔融的PC材料從擠出機的模頭中擠出,并通過特定的模具形狀冷卻固化,形成所需的型材截面。模具的設計和精度決定了產品的形狀和尺寸精度。
- 定型與冷卻:新擠出的產品需要通過定型裝置來確保尺寸穩定,隨后進入冷卻水槽或風冷系統進行快速降溫,以提高制品的機械強度和尺寸穩定性。
- 切割與檢驗:冷卻后的產品根據需求長度進行切割,并進行質量檢驗,包括尺寸、外觀及物理性能等指標的檢查,以保證產品質量符合標準。
- 包裝與儲存:合格的PC型材將被適當包裝,并儲存于干燥通風的環境中,避免受潮或陽光直射造成質量下降。
通過對PC擠出機生產工藝流程的了解,可以看出每個環節都至關重要,不僅影響產品質量,也關系到生產成本和效率。因此,企業在操作過程中需嚴格控制各個環節,確保整個生產線的順暢運行,從而在競爭激烈的市場中占據有利地位。
TAG: